Freightliner
Revolutionising rail safety
Adopting Work Wallet's digital health and safety management tools has helped Freightliner to improve safety standards at its busy south coast depot - delivering essential safety briefings, streamlining asset inspection, and managing contractors and visitors more efficiently.
completed
completed
briefed
completed
saved so far
Identifying the problem
Identifying
the problem
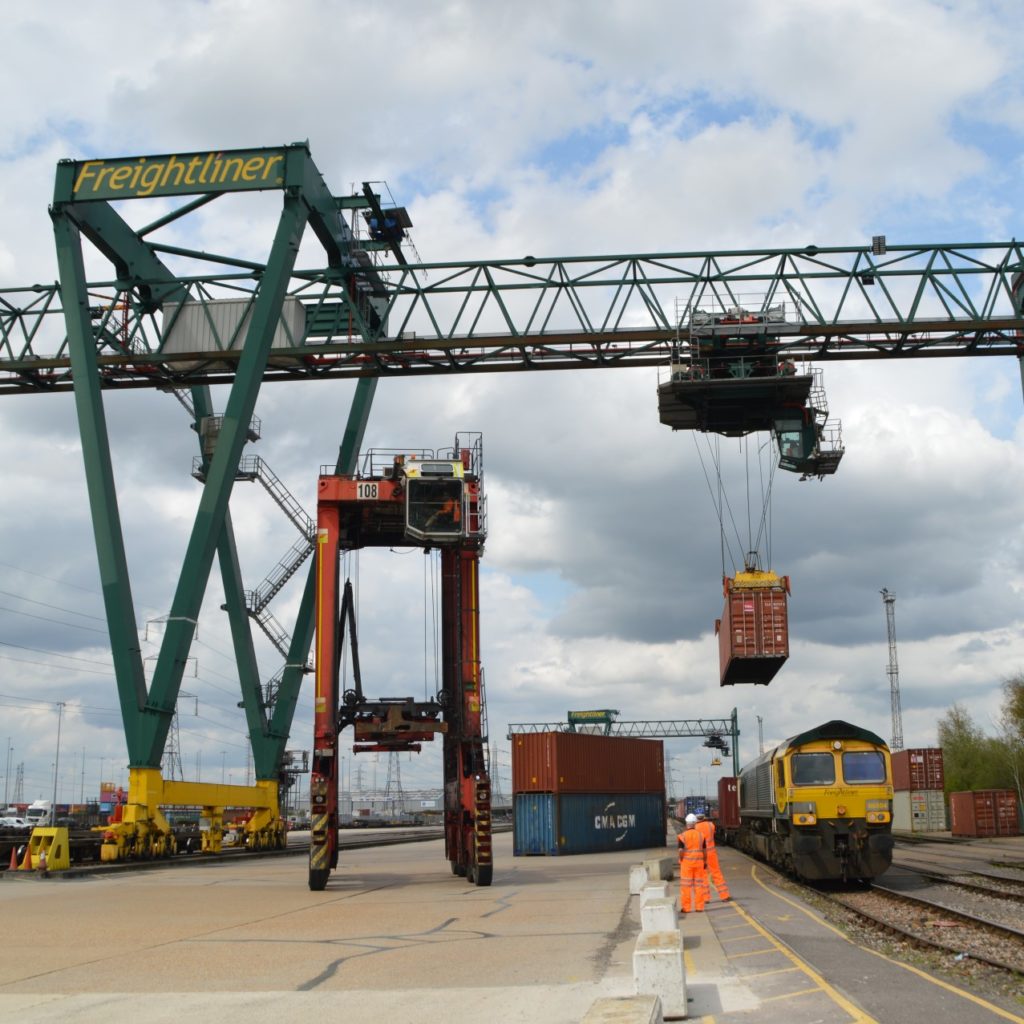
In such a busy environment, health and safety needs to be a top priority. Freightliner Southampton identified that its traditional paper-based briefing processes were inadequate. This meant employees and site visitors could miss essential safety information. Sometimes information could take too long to share, making it out of date.
With a mix of extremely large and heavy plant equipment on site too - including trains, cranes and reach-stackers - equipment failure is not an option, from both safety and operational productivity perspectives. Freightliner Southampton needed a way to speed up asset inspections, keep better track of maintenance issues, and schedule repairs.
"Using Work Wallet has allowed Freightliner Southampton to vastly improve on our previous briefings delivery method and our controls. Overall, moving from paper to digital has significantly improved staff communication, as well as making on-site contractor safety, document control and job assignment better."
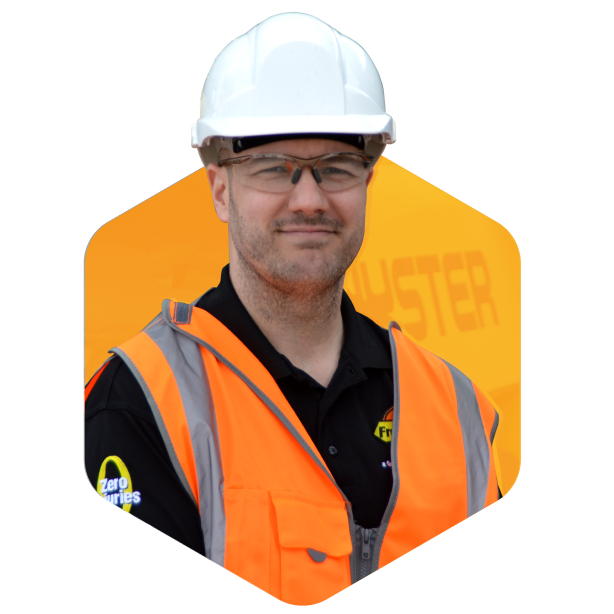
Finding the solution
Finding
the solution
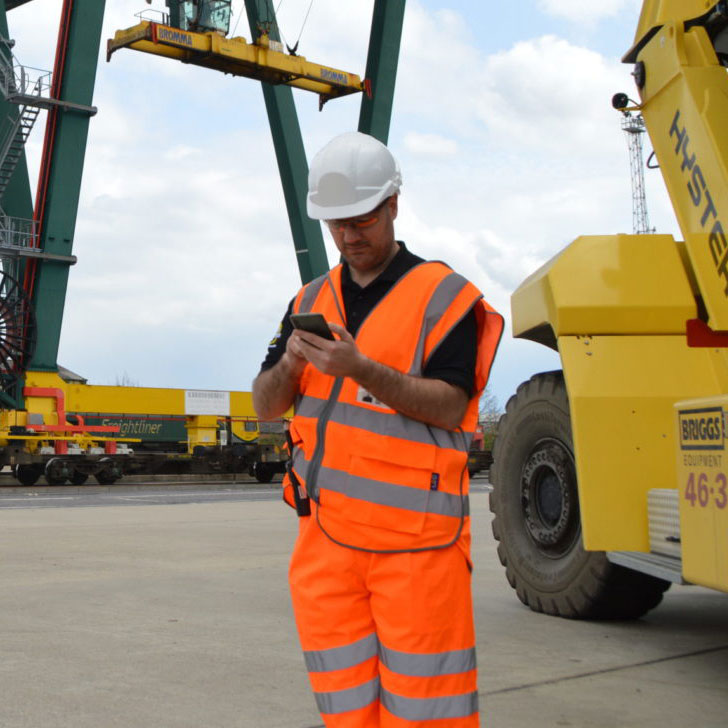
Embracing paperless working, Freightliner Southampton reviewed and trialed the diverse options available on the market to digitise its health and safety processes. After detailed comparison with competing platforms, they identified Work Wallet as the system that would benefit Freightliner the most.
In particular, they wanted a system with easy-to-use and simple-to-learn interfacing, which could be rolled out at the depot quickly and with minimal fuss, and remove the need for paper files. Employees also needed to be able to manage processes from the site office or use it on-the-go on the depot floor, with seamless communication between the two that would help build a stronger safety culture.
The flexibility to choose specific modular solutions as required, from the wider suite of Work Wallet products, at an affordable price, was a big bonus.
"I find the app really easy to use. I use it for safety checks on the machines, and getting safety briefings, and it has helped us a lot."
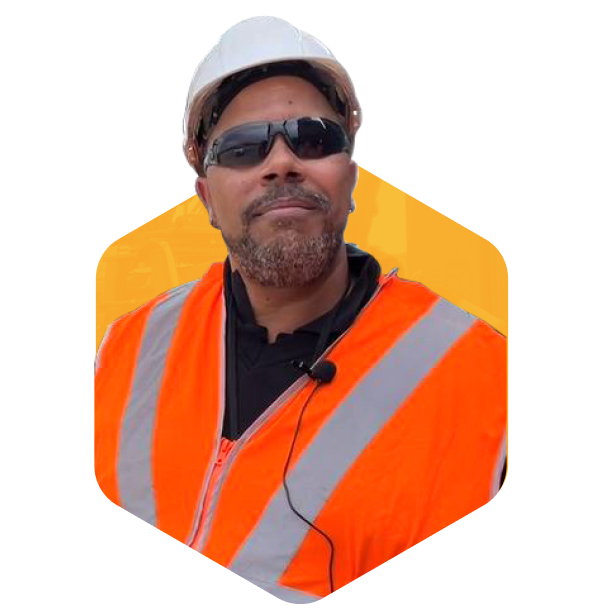
Delivering the outcome
Delivering
the outcome
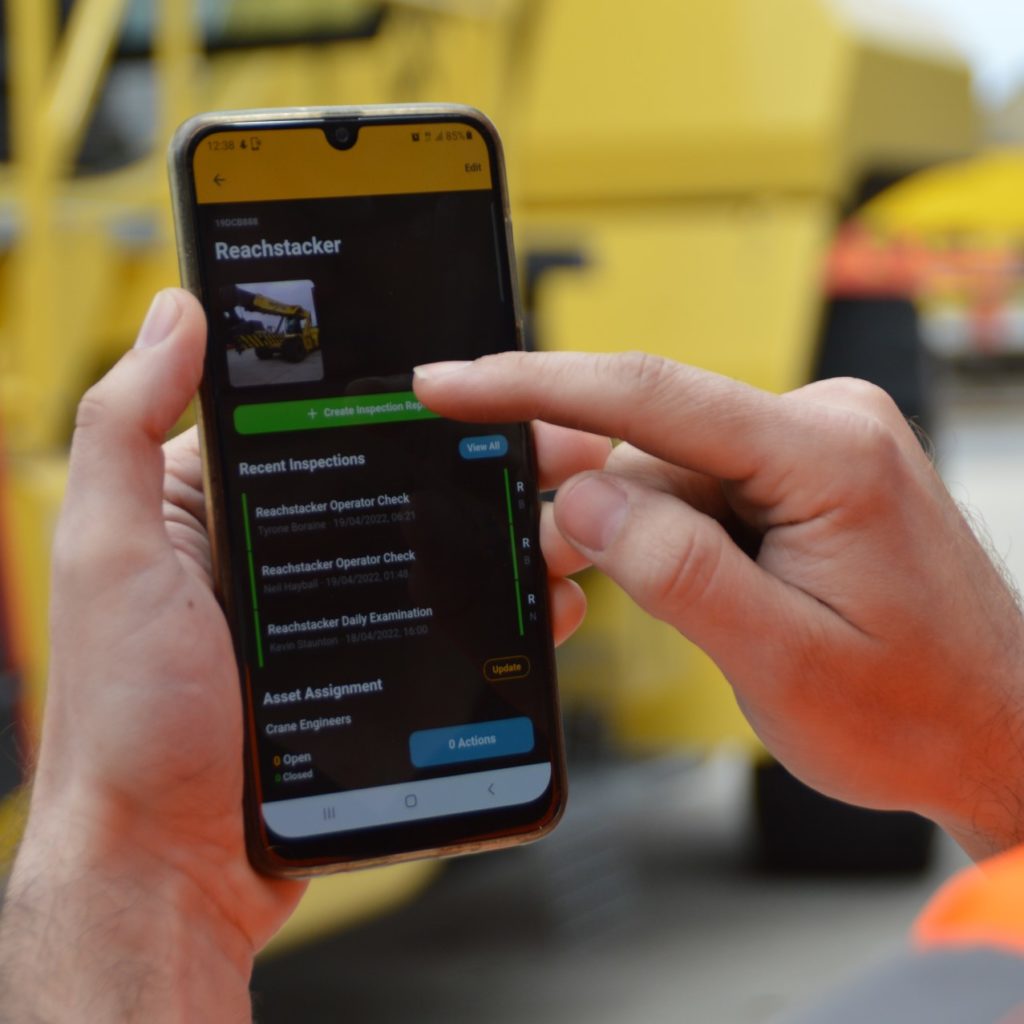
Freightliner Southampton now uses Work Wallet to deliver its safety briefings instantly, and to monitor and track responses and acknowledgements of its key messages. Messages which could have previously taken hours to filter through to employees now reach them in a matter of seconds, and Shane can see they have been received and understood.
Employees out on site at the depot are able to check the assets they use more easily. Each asset has a designated QR code that can be scanned with a smartphone or tablet, allowing it to be verified as fit for use after a physical inspection. Users can also report defects in real-time for repair or rectification, and assets can be scheduled for regular maintenance more easily with built-in alerts.
Want to know more?
You've seen how successful our customers are by using Work Wallet's digital safety tools.
See how we can improve your business health and safety.
Book a personalised demo with our experts to discover how our technology can help your business.
You can also reach us by email at [email protected] or phone on +44(0)1332 505252.
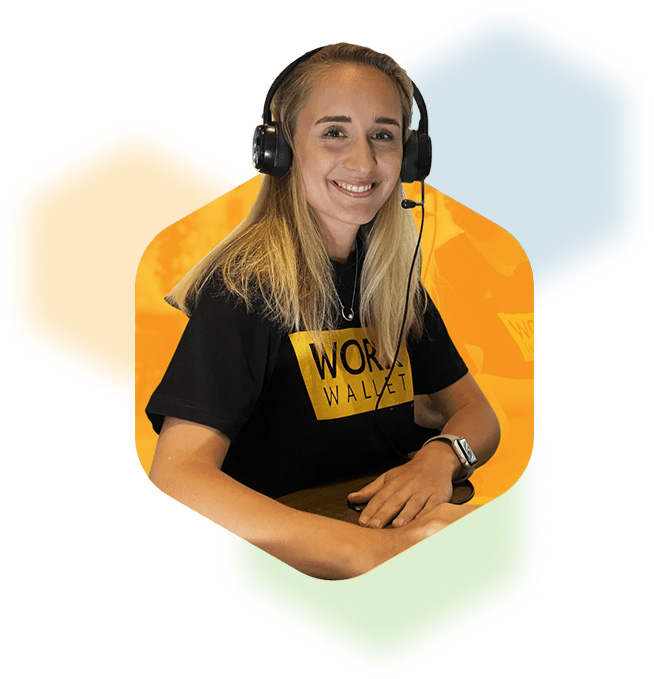